У кінці бронзового віку людство почало створювати сплави на основі заліза. Настав залізний вік. Тисячоліттями удосконалювалися технології лиття чавунних гармат і різних механізмів, виготовлення сталевих клинків. Алхіміки і хіміки виділяли з природних мінералів металеві з’єднання і відкривали нові метали, виникла і розвивалася металургія – наука про виробництво металів.
З ХVII століття розгорнулася промислова індустріалізація. Для техніки, заснованої на енергії пари, для нових видів транспорту, мостів та промислових будівель та іншої нової техніки знадобилося багато металу, в першу чергу, багато високоякісної сталі.
Ці завдання вирішували «методом проб і помилок», а з кінця XIX століття – і на основі фундаментальних наукових досліджень. Металурги, крім хімічних процесів, для нагрівання і плавлення почали застосовувати електричну енергію.
Але темпи науково-технічного прогресу продовжували рости. У другій половині минулого століття створювалися ракети, атомні електростанції, супер винищувачі, потужні турбіни, нові класи кораблів і багато іншого, невідомого й немислимого.
Техніка нового покоління працювала за умов надвисокого тиску і струсів, небачених раніше високих і, навпаки, дуже низьких температур і за умов інших екстремальних навантажень.
Звичайно, металурги продовжували створювати нові спеціальні типи сталей. Наприклад, для підвищення жароміцності додали в сплав вольфрам, ванадій, молібден.
Але сталь від цього ставала ще важчою. А маса багатьох машин і апаратів повинна бути якомога меншою. Були потрібні сплави, міцніші за сталь, жаростійкі і кріогенностійкі, нержавіючі, і такі, що не руйнуються в агресивних середовищах.
У першій половині минулого століття вже почали широко застосовувати легкий метал алюміній і його сплави. І хоча міцність їх була набагато менша, ніж у сталі, вони виявилися дуже корисними для створення легких конструкцій, навіть таких складних як літаки, дирижаблі та деякі кораблі.
Алюміній і його сплави не іржавіють і не роз’їдаються майже ніякими кислотами, тому з них виготовляють хімічне обладнання, різне приладдя. В електротехніці чистий алюміній став у пригоді через хорошу електропровідність, а сплав алюмінію з кремнієм має відмінні ливарні властивості: з нього відливають корпуси двигунів внутрішнього згоряння для автомобілів і літаків. Але алюмінієві сплави – порівняно легкоплавкі.
Необхідно було знайти метал і створити з нього сплави, кращі і легші за сплави із заліза.
І такий метал знайшовся. Причому, якщо залізна руда і боксити (сировина для алюмінію) сконцентровані у певних покладах, то сировина для металу, що відповідає вимогам науково-технічного прогресу, знайшлася буквально «під ногами» у вигляді піску або у вигляді руди.
Згадаймо, що земна поверхня складається із з’єднань металів і неметалів, ними вкрите дно морів і океанів, вони розчинені в морській воді. Ось тільки виділити метал з його сполук буває зовсім не просто. І надбання людства на тисячолітньому шляху пошуків металургійних технологій, не завжди ставали у нагоді для того, щоб «добути» новий метал і організувати його виробництво. Ось і над приборканням дуже потрібного для сучасної техніки металу фахівці працюють вже більше двохсот років.
Одним з поширених занять хіміків минулих століть було визначати склад «земель», що траплялися їм. У 1791 році англієць У. Грегор, досліджуючи склад магнітного залозистого піску з Корнуольского пляжу, виділив нову «землю» (оксид) невідомого металу.
А через чотири роки незалежно від нього німець Мартін Генріх Клапрот (1743-1817) відкрив у мінералі рутил новий елемент. Німецький дослідник зазначив неможливість визначення властивостей нового елемента тільки за його оксидом і назвав його титаном – на честь стійких борців з богами Олімпу з давньогрецької міфології. Трохи раніше він же відкрив метал, який назвав ураном.
Клапрот встановив, що рутил і «земля Трегор» – оксиди одного і того ж хімічного елемента, за яким і залишилася назва «титан». У вільному вигляді титан не зустрічається, але знаходиться на 10-му місці за поширеністю в природі: в рутилі, ільменіті, перовськиті, інших мінералах і в морських глинистих відкладаннях.
Перший зразок металевого титану вдалося виділити з оксиду в 1825 році хіміку Каролінгського університету (Швеція) Йенсу Якобу Берцеліусу. Однак його спосіб був настільки складним, а сам титан виявився настільки хімічно активним, що ніхто не побачив перспективи в його застосуванні.
Тільки через 100 років голландці А. Ван Аркел та І. Де Бур в 1925 році, застосувавши технологію термічного розкладання парів йодиду титану (TiI4), нарешті отримали чистий титан.
Цей спосіб застосовують для отримання невеликих кількостей титану дуже високої чистоти (до 99,99%). Титанову губку кладуть у реторту і нагрівають до 100-200 °С, потім всередину реторти вводять і розбивають ампулу з йодом, що взаємодіє з титаном (реакція Ti+2I2=TiI4). (В принципі можна застосовувати і інші галогеніди).
Розкладання TiI4 на Ti+2I2 і виділення титану відбувається на титанових дротах, натягнутих в реторті, нагрітих до 1300-1400 °С пропусканням струму.
Було встановлено, що титан – легкий міцний метал сріблясто-білого кольору. Температура його плавлення 1660°С, точка кипіння 3260 °C. Метал існує у двох модифікаціях: α-Ti і β-Ti, щільність яких відповідно дорівнює 4,505 і 4,32 г/см3. Між іншим, титановий пил за температури 400 °С вибухає. Пожежонебезпечна і титанова стружка.
Ряд особливих фізикохімічних властивостей титану, насамперед висока питома міцність (відношення міцності до питомої ваги), велика корозійна стійкість у багатьох агресивних середовищах, хороша оброблюваність тиском та інші цінні технологічні властивості роблять його незамінним.
Дійсно, в середині минулого століття науково-технічний прогрес без титану і його сплавів почав «пробуксовувати». І довелося, не рахуючись із витратами, шукати способи промислового виробництва найважливішого матеріалу.
Спочатку спробували виплавити титан так, як виплавляють із залізних руд чавун. Концентрат титанової руди почали плавити в суміші з деревним вугіллям або антрацитом в електродуговій печі і отримали шлак з окису титану і різних домішок.
Але «відібрати» кисень у титану не просто, тому на другому етапі вирішили використати більш активний елемент – хлор.
У спеціальну піч, у нижній частині якої нагрівається вугільна пластина за допомогою пропущеного крізь неї електричного струму, завантажують титановий шлак, а через фурми задувають хлор. І при температурі 800-1250°С утворюються пари чотирихлористого титану, а також хлориди інших домішок. Пари очищають від твердих частинок, охолоджують у конденсаторах і отримують рідкий чотирихлористий титан.
Експериментатори знайшли й інші способи отримання титану. Не будемо їх описувати детально. Зазначимо тільки, що отримати чотирихлористий титан можна в хлоратоpax безперервної дії, в сольовому розплаві; в киплячому шарі.
А наукову основу третього етапу – термітні реакції – заклав Бекетов Микола Миколайович (1827-1911) («Страна Знаний», 2015 №4).
Магнієтермію виконують у герметичних реакторах (ретортах) із нержавіючої сталі, встановлених в електричних печах опору.
З реторти відкачують повітря, заповнюють її інертним газом аргоном, заливають туди розплавлений магній і поступово – рідкий чотири-хлористий титан. Титан відновлюється магнієм в реакції TiCl4+2Mg=Ti+2MgCl2 з виділенням великої кількості тепла.
Необхідна за технологією температура 800... 900°С підтримується в реакторі дозованою подачею TiCl4. (Замість магнію іноді застосовують і натрій, і цей спосіб відновлення називають натрієтермічний.) Правда, на жаль, виходить не щільний злиток, а пориста титанова губка (до 60% Ti). (Чи не правда, з подібним залізним «напівфабрикатом» – крицею мали справу металурги-ковалі в давнину? («Страна Знаний», 2015 № 3)).
На жаль, проковуванням цієї губки чистий титан отримувати не вдавалося. Необхідно було розробляти ще одну технологічну операцію – переплавляти цю «суміш» так, щоб позбавити її від домішок.
Розпочався наступний етап «боротьби людини з титаном». Тепер з губчатого титану треба було виплавити щільні, без пор і включень металеві заготовки для прокату або виливків. В середині ХХ століття перед світовою металургією відкрився черговий етап підкорення норовливого металу – доведення його до потрібних для нової техніки якостей.
Результати робіт тримали у секреті – основними замовниками були творці нової військової техніки. Розв’язанням завдань переплаву і зварювання в принципі і стосовно до конкретного виробництва займалися десятки інститутів і лабораторій в СРСР, США, Великобританії, Франції та ще в деяких країнах.
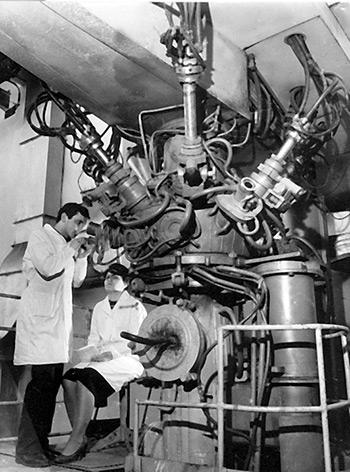
переплаву в ІЕЗ ім. Є.О.Патона
Працювали інтенсивно – гонка озброєнь вже набрала обертів. Роботи з дослідження і розробки металургійних і зварювальних процесів стосовно до титану були розпочаті в Інституті електрозварювання ім. Є.О. Патона (ІЕЗ) НАН України наприкінці 50-х років минулого століття під загальним керівництвом академіка Бориса Євгеновича Патона.
І незабаром у Києві вперше в світі були розроблені найефективніші технології отримання зливків титану і його сплавів із первинної шихти і з вторинних відходів. Для вирішення проблеми знадобилися знання, накопичені в процесі створення нових зварювальних технологій і електрошлакового переплаву.
Співробітники застосували енергію електронних променів, дугової плазми, індукційний і електрошлаковий нагрів. Кожен з процесів має свої переваги і використовується для виробництва металу з конкретними властивості, саме такими, які потрібні для відповідальних конструкцій.
Потужний електронний промінь плавить заготовки у вакуумі під тиском 0,1 ... 0,01 Па. Технологічні процеси забезпечують видалення сторонніх домішок і розчиненого газу, дозволяють отримувати зливки титану і його сплавів з однорідною бездефектною структурою. Для їх впровадження було створено сімейство багатоцільових промислових плавильних електронно-променевих установок .
У плазмодугових електропечах заготовки розплавляють одним або декількома дугами, стислими потоками аргону в плазмотронах. Плазменно-дугова піч дозволяє виплавляти титанові зливки безпосередньо із кускової шихти (губчастого титану), минаючи операцію пресування заготовок.
Одним з найбільш універсальних незалежних джерел нагріву є високочастотне магнітне поле, створюване електричним струмом в індукторі.
Особливості індукційного нагріву, у тому числі інтенсивне перемішування рідкого металу, гарантує вирівнювання хімічного складу, можливість витримувати метал у рідкому стані необмежений час у вакуумі, забезпечують високу якість виливків.
Альтернативою переплавам у вакуумних умовах є електрошлаковий переплав. Для нього не потрібно такого складного обладнання, суворого дотримання режиму плавки, і при досить високій якості собівартість робіт найнижча. Найкращої якості вдається досягти в печах камерного типу.
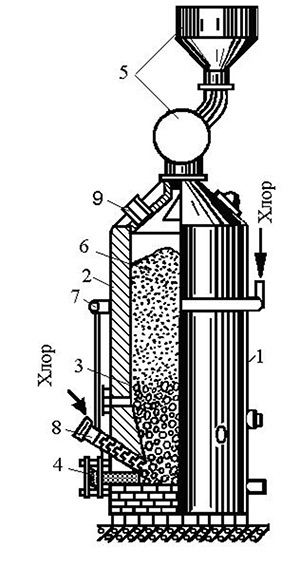
отримання чотирихлористого титану:
1 – корпус печі;
2 – футеровка;
3 – вугільна набойка – електроспротив;
4 – струмопідводящі
графітові електроди;
5– пристрій для завантаження шихти;
6 – брикетована шихта;
7, 8 – патрубки для подачі хлору;
9 – отвір для видалення
парогазової суміші.
У ІЕЗ була розроблена технологія магнітокерованої електрошлакової плавки для виробництва сплавів титану з будь-якою великою кількістю компонентів. Найбільш істотними перевагами цієї технології є можливість рафінування низькосортної дешевої сировини від шкідливих домішок, висока щільність литва, менші витрати технологічної електроенергії і порівняно дешевше обладнання.
І чим дешевшим ставало виробництво титану і сплавів з якостями, необхідними для відповідальних виробів, тим більшою була в них потреба. Тільки в СРСР за короткий час виробництво титанової продукції було налагоджене на двох десятках заводів.
Для економії дорогого металу в конструкціях, де важливішою була стійкість до агресивних середовищ, ніж вага виробу, використовувався біметал. У 1980-х роках було освоєно виробництво біметалевих листів шляхом гарячої прокатки заготовок. Найкращим матеріалом для них виявилася композиція сталь + титан, тобто сталь, плакована (покрита) титаном.
В ІЕЗ ім. Є.О. Патона відкрито цех «Титан», який може випускати до 1500 т титанових зливків на рік для прокату високоякісних напівфабрикатів.
З таких сплавів товщиною 200 ... 250 мм на Феодосійському суднобудівному заводі «Море» були виготовлені крильові пристрої для морських суден. У 2009 році була створена технологія електронно-променевої плавки великогабаритних зливків жароміцних сплавів на основі титану.
Вперше у світі отриманий злиток жароміцного титанового сплаву ВТ3-1 діаметром 840 мм, а незабаром був отриманий зливок діаметром 1100 мм, довжиною до 4000 мм, масою 16 тонн.
Вперше у світовій практиці в цеху «Титан» спроектована, виготовлена і запущена в експлуатацію електронно-променева установка для отримання титанових зливків недроблених блоків губчастого титану.
Для виготовлення атомних і хімічних реакторів в ІЕЗ ім. Є.О. Патона налагоджено виробництво порожнистих зливків, з яких розкочують титанові кільця діаметром до 2000 мм.
Вперше у світі були виготовлені безшовні титанові труби довжиною до 9000 мм із трубної заготовки.
Усе більше застосування у цивільних галузях промисловості знаходять як традиційні титанові сплави, так і нові титанові сплави з унікальними фізико-хімічними характеристиками. Титан є одним із найбільш поширених геттерних матеріалів, використовуваних у в високовакуумних насосах.
Детальне вивчення корозійної стійкості сплаву Т100 в різноманітних агресивних середовищах, у тому числі і в біологічних, показало його перспективність для застосування в медицині для виготовлення ендопротезів та медичного інструменту.
Для потреб стоматології в ІЕЗ ім. Є.О. Патона розроблений титановий сплав системи Ti-Al-Nb-Zr.
Одним із найважливіших споживачів титанових сплавів в Україні є аерокосмічний комплекс. У конструкціях літаків маса деталей з титанових сплавів становить 8 ... 9% маси планера. Це, головним чином, важко навантажені силові елементи, такі як підкоси і циліндри шасі, кронштейни системи управління, деталі механізації крила, протипожежні перегородки, вантажні доріжки настилу.
З титанових сплавів виготовляють трубопроводи, теплообмінники, компенсатори та інші вузли літаків.
У хімічній, харчовій промисловості із сплавів титану роблять реактори, трубопроводи, насоси, трубопровідну арматуру, опріснювальні установки та ін.
Першою у світовій практиці монументальною скульптурою з титану є пам’ятник Юрію Гагаріну на площі його імені в Москві.
Титанові сплави мають найбільш високу питому міцність серед усіх металевих матеріалів. Титан використовують для легування сталей і створення спецсплавів. Розроблено безліч сплавів титану з різними металами. Нитинол (нікель-титан) – сплав, що має пам’ять форми, і застосовується в медицині і техніці.
Алюмініди титану є дуже стійкими до окиснення та жароміцними. Карбід, диборід, кабонітрид титану — важливі компоненти надтвердих матеріалів для обробки металів.
Титанові сплави застосовуються у виробництві спортивних товарів, мобільних телефонів, годинників, а також бронежилетів.
Будь-які метали, кераміку, скло та багато інших матеріалів можна вкрити нітридом титану, що має колір золота. Але, на відміну від золота, це надтонке покриття дуже міцне та набагато дешевше, ніж золоте. Ця технологія була розроблена у Фізико-технічному інституті у Харкові й широко застосовується для покриття інструментів, зубних коронок, посуду, куполів церков та виробів біжутерії.
А найбільшими у світі зварними конструкціями з титанових сплавів є малошумні важкі ракетні підводні крейсери стратегічного призначення (ТРКСН проекту 941, шифр «Акула», за класифікацією НАТО – «Typhoon»).
Перший з 12 кораблів був побудований в Северодвінську на «Севморзаводі» у вересні 1979 року за технологіями, розробленим в ІЕЗ ім. Є.О. Патона.
Ніде в світі немає підводних кораблів водотоннажністю 28500 т, довжиною 172,8 м, шириною 23,3 м. Цей крейсер може занурюватися на глибину 500 м і йти там зі швидкістю 27 вузлів.
Конструкція ТРКСН виконана за типом катамарана з двох роздільних міцних корпусів (діаметр кожного 7,2 м), між якими розташовані відсіки управління, торпедний і ракетний.
Використання титанових сплавів дозволило зменшити масу корпусу, збільшити глибину занурення, зменшити магнітне поле. Звичайно, і в країнах НАТО є титанові човни, але їх тактико-технічні дані гірші.
Незважаючи на явні успіхи у підкоренні титану, вчені продовжують удосконалювати його виробництво, а конструктори та інженери – створювати нову техніку.
Зараз світове виробництво титану складає біля 4500000 т. на рік. При нинішніх темпах застосування (використання) світових розвіданих запасів титану вистачить більш, ніж на 150 років.
А.П. Лютий, кандидат технічних наук, завод «Дніпроспецсталь», м. Запоріжжя